Один из докладчиков – заместитель генерального директора ООО «АКЕ-РУС» Владимир Падерин проанализировал итоги семинара и подготовил краткий обзор рекомендаций по эксплуатации круглопильного инструмента и его обслуживанию на мебельном предприятии.
Затраты на режущий инструмент в цеховой себестоимости продукции, в частности, на мебельных производствах, как правило, не превышают 1-3%. Если они выше, нужно выявлять причины возникновения проблемы.
Основные факторы, которые влияют на расходы, связанные с приобретением, обслуживанием и работой режущего инструмента, это:
- Подбор режущего инструмента, исходя из соотношения «цена – качество»;
- Правильное применение режущего инструмента, в зависимости от оборудования и технологии;
- Оптимальный выбор сервисного центра или собственного качественного заточного оборудования;
- Состояние основного технологического оборудования;
- Уровень общей культуры производства;
- Наличие обученного и квалифицированного технического и технологического персонала;
- Организация хранения, учета и обслуживания режущего инструмента.
Приобретая инструмент, нельзя ориентироваться на самый дешевый. Ведь каждый производитель в условиях постоянной конкуренции стремится снизить стоимость своей продукции до разумного минимума, поэтому ее высокая цена всегда чем-то оправдана. Так, можно предположить, что из двух пил, одинаковых по форме и количеству зубьев. Выгоднее приобретать ту, у которой пластины зубьев длиннее и толще, - ведь по сравнению с другой пилой можно рассчитывать н большее число заточек при стандартном съеме 0,1 – 0,15 мм . Другой пример. Пилы изготавливают из разных сортов и видов стали. Без практики также трудно понять, какая из них лучше. Это определяется, к примеру, когда в результате усталостных напряжений корпус пилы пойдет трещинами или подгорит, и инструмент станет непригодным к работе или перенапайке. Поэтому к выбору дереворежущего инструмента нельзя подходить бездумно.
Выбирать инструмент надо под конкретные задачи. Учтите: выбор пилы с определенным количеством зубьев рекомендованной формы профилей и угловых параметров не означает, что она будет сразу и долгое время работать эффективно .
Рассмотрим одну из важнейших характеристик процесса пиления круглыми пилами – подачу на зуб (коэффициент подачи u z ) существуют три формулы расчета коэффициента подачи на зуб: в зависимости от мощности привода станка, качества получаемой поверхности (статья «ЗА» и «ПРОТИВ» - показатели качества инструмента. Как правильно подойти к выбору нужного Вам инструмента» ) и объема межзубной впадины. Поскольку расчетная (рабочая) скорость подачи выбирается из наименьшего из трех значений u z и производственники не обращают на это значение никакого внимания (иак как первые две формулы довольно хорошо им известны), приведем здесь формулу для расчета uz .
Формула для расчета подачи на зуб стандартных пил по допустимому коэффициенту заполнения межзубных впадин опилками при пилении круглыми пилами:
![uz=t2/[(4...5)]Hmax uz=t2/[(4...5)]Hmax](images/new_technologies10/uz.jpg)
Где
t – шаг зуба, мм;
H max – максимальная высота пропила, мм;
4 – принимается для пилы с углом резания ? = 65
градусов
и задним углом ? = 20 градусов;
5 – для пилы с углом резания ? = 60 градусов и задним углом ? = 15 градусов.
Некоторые производители режущего инструмента не учитывают этого момента (объема межзубной впадины), слепо копируя известные бренды, что в дальнейшем, после нескольких переточек зубьев пил, приводит к тому, что пила перестает пилить как новая, например, несколько листов плит одновременно, так как опилки переполняют межзубную впадину и процесс пиления прекращается. В этом случае надо после пяти-семи переточек дорабатывать межзубную впадину, или уменьшать высоту пропила, или снижать скорость подачи. Доработку впадины, если нет специального оборудования, в условиях предприятия выполнить практически невозможно, поэтому целесообразно снизить скорость подачи и (или) уменьшить высоту пропила.
В случае быстрого появления сколов при пилении следует переточить пилу правильно, с соблюдением всех режимов заточки, на хорошем заточном оборудовании. Если положительного результата нет, то проблемы здесь может быть две: изначально низкое качество пилы и ее неправильная заточка в процессе эксплуатации (например, если заточка выполнена только по задней грани либо при заточке не использовалась СОЖ и т.п. ).
Учитывая то, что подача на зуб определяет выбор рабочей скорости подачи и производительность оборудования, а в конечном счете и себестоимость продукции, значение этого коэффициента переоценить трудно.
- Невозможно выполнить пакетную (в несколько листов) обработку – для этого необходимо более производительное оборудование.
Отдельная проблема – определить, какое именно количество инструмента должно быть в ходу на предприятии. Самый простой ответ: на станок надо как минимум три комплекта : один устанавливается на станок и эксплуатируется, второй хранится на складе инструмента, а третий находится в заточке.
Но если инструмент необходимо менять раз в две – три смены, а на его заточку сторонней организацией уходит неделя или больше, то количество комплектов должно быть увеличено. Причем следует учитывать, что за одно и то же время работы разный инструмент затупляется неодинаково. Так, у подрезной пилы диаметр и число зубьев меньше, чем у сопряженной с ней основной. Подрезная работает с попутной подачей, что связано с большой ударной нагрузкой на передние грани ее резцов. Зубья этой пилы выполняют закрытое резание, затрудняющее отвод стружки, в зоне пылевидного слоя ДСП или MDF , а также пленки и клеев. Зачастую в плитных материалах содержится большое количество инородных тел, например, песчинок, что приводит к быстрому затуплению лезвий. Поэтому подрезная пила меняется минимум в два раза чаще основной, и это надо обязательно учитывать при расчете необходимого количества инструмента.
Еще одна проблема – как своевременно определить, что инструмент затуплен и его пора отправлять на переточку? Работа затупленным инструментом недопустима: падает качество обработки и снижается ресурс инструмента из-а необходимости снятия большего слоя его режущей части при заточке.
Обычно опытный станочник сам определяет, когда инструмент затупляется. Лучше, если на предприятии могут быть созданы нормативы времени эксплуатации инструмента до переточки, основанные, например, на количестве обработанных погонных метров деталей.
Многие компании стараются приобрести дешевый станок для заточки дереворежущего инструмента. Это хорошая идея, но только в том случае, если на нем будут затачиваться пилы для собственного производства, с минимальными съемами твердого сплава и минимальной скоростью подачи, заточником, понимающим специфику заточки и те проблемы, которые могут появиться. Ведь подготовка заточка дереворежущего инструмента – сложнейший комплекс операций, требующий использования не только специальных заточных станков, но и высокоточного измерительного инструмента. У пил, оснащенных пластинами твердого сплава и заточенных на станке, которые изготовлены, например, в станах, где традиции производства заточных станков сформировались в последние пять-десять лет, стойкость до следующей переточки в два раза ниже, чем у новых или заточенных грамотными и опытными специалистами на профессиональном оборудовании. Поэтому иногда целесообразно посчитать, что дешевле: собственный заточной участок или сервисный центр, находящийся в 300 км от предприятия.
При этом следует понимать, что ни в одном справочнике сегодня нельзя найти данные об углах заточки лезвий пил и фрез, используемых для эффективной и качественной обработки различных древесных материалов. Например, для стандартной и влагостойкой плит MDF требуются инструменты с разными характеристиками. По-хорошему, они известны только изготовителю инструмента, разработавшему его конструкцию и знающему особенности материалов, из которых он изготовлен. А иногда требуется опробование и доводка инструмента на каждом предприятии, оборудовании и при определенных перерабатываемых плитных материалах.
Многим производителям мебели хорошо известно, что древесные плиты, выпускаемые на одном предприятии, облицованные одинаковыми материалами, но разного колера и текстуры и изготовленные в разные дни, ведут себя при раскрое по-разному. На одних плитах пилы работают длительное время, на других – требуют замены уже после нескольких минут работы. Толщина пленок (меламина), расход клеевых материалов, плотность плит, то, из каких пород они сделаны, - все это факторы, которые могут серьезно повлиять на стойкость режущего инструмента, а следовательно, и на производительность оборудования. Кстати, при обработке древесных плит (ДСП и MDF), облицованных пленками на основе термоактивных смол (ламинированных), все лезвия инструмента должны быть оснащены пластинками твердого сплава (HM) или сверхтвердых материалов (искусственного алмаза).
Подготовку и заточку своего дереворежущего инструмента можно доверять только профессионально оснащенным сервисным предприятиям, предварительно убедившись в наличии у них высококлассного оборудования и обученных специалистов. Нюансов много, например, дисковые пилы с режуще частью из твердого сплава затачиваются по задней и передней граням в соотношении 3:1, то есть по задней грани съем твердого сплава должен быть, например, 0,3 мм, а по передней – 0,1 мм. Только правильно заточенные дисковые пилы сохраняют свою производительность на протяжении всего срока службы. Неправильная заточка (только передней или только задней грани) влечет за собой резкое уменьшение срока службы. Важно, чтобы при заточке затупившейся пилы изношенный слой металла был полностью снят и радиус режущей кромки не превышал 5 мкм. Твердосплавные дисковые пилы качественно затачиваются на автоматических шлифовальных станках и с использованием охлаждающей жидкости. Заточка дисковых пил вручную на универсальных шлифовальных станках не рекомендуется по причине низкого качества обработки режущих элементов. На автоматических заточных станках возможна заточка всех форм зубьев (по одному проходу на каждую грань).
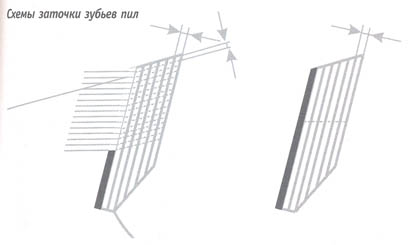 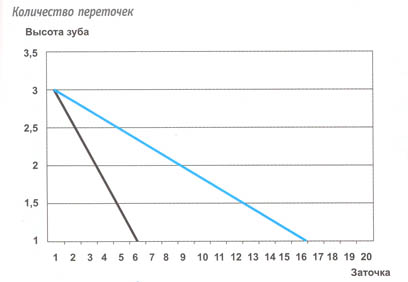
На рисунках представлены схемы заточки зубьев пил и диаграмма, содержащая информацию о количестве переточек, при заточке по задней и передней граням раздельно. Затачивание по передней и задней граням гарантирует оптимальное использование твердосплавных зубьев и обеспечивает стабильно длительный срок службы между заточками. Из соображений безопасности минимальная остаточная высота зуба составляет 1 мм (если измерять от основания зуба).
Если еще пять – шесть лет назад алмазный инструмент на российских мебельных предприятиях был редкостью, то сегодня многие перешли не только на алмазные фрезы, но и на алмазные пилы. Но подобный инструмент становится все более сложным как по конструкции, так и по технологии применения. Чтобы поддерживать его в работоспособном состоянии, нужен хорошо организованный сервис в специализированной организации.
Только за счет повышения качества обработки деталей изготавливаемой мебели, а также стойкости и долговечности (ресурса) инструмента, кажущиеся многим мебельным предприятиям излишними затраты на его покупку и обслуживание окупаются очень быстро.
Есть и еще одна проблема, так и не решенная на многих наших предприятиях. Она заключается в том, чтобы установить, кто именно должен отвечать за хранение дереворежущего инструмента, ведь может случиться, что какой-то нечестный работник прикарманит алмазную фрезу, стоимость которой превышает размер его месячной зарплаты, чтобы сбыть за полцены соседям-конкурентам. Для строгого учета инструмента может пригодиться система, когда-то использовавшаяся на некоторых советских предприятиях: станочникам под расписку выдают металлические марки, на которых набит их табельный номер. Рабочий отдает кладовщику инструментально-раздаточной кладовой свой жетон и называет нужный ему инструмент. Выдав инструмент, кладовщик кладет на то место, где лежал данный инструмент, этот жетон. На станок инструмент обычно устанавливают сами станочники, с помощью наладчиков, которые одновременно выполняют и настройку сложных станков. После возврата инструмента на склад рабочий получает свой жетон обратно. Подобная система значительно снижает риск потери или кражи инструмента.
Кладовщик или другое ответственное лицо могут так же вести журнал, в который заносится информация о рабочем месте, типе выданного инструмента, времени его выдачи и возврата, а также о его техническом состоянии и числе переточек, выполненных ранее. Анализ записей в журнале позволяет судить о своевременности съема затупившегося инструмента с оборудования, учитывать случаи аварийного выхода инструмента из строя или его вынужденной замены. На основании сведений из этого журнала формируется комплект инструмента, направляемого на переточку. Для удобства и простоты ведения учета и контроля расходования инструмент целесообразно маркировать, например, лазером или электроискровым способом.
Конечно, отдельные из приведенных здесь советов – прописные истины для некоторых производственников. Но в том-то и проблема, что они не выполняют даже этих элементарных правил. Поэтому на каждом предприятии сегодня важно создать жесткую систему обращения дереворежущего инструмента, включающую понятный порядок действий при его учете, подготовке, заточке, эксплуатации и хранении.
Остановимся на некоторых технических аспектах сервиса круглых пил для форматно-раскроечных станков.
РЕСУРС И СТОЙКОСТЬ РЕЖУЩЕГО ИНСТРУМЕНТА
Довольно часто у клиентов сервисных центров возникают вопросы: почему отдельный инструмент не выдерживает количество заточек, указанных производителем, и почему стойкость пил после заточек падает? Чтобы ответить на них, следует рассмотреть все факторы, от которых зависит стойкость режущего инструмента, на примере процесса заточки дисковых пил для форматно-обрезных станков. Вот эти факторы:
- Качество плитного материала;
- Качество твердого сплава;
- Соблюдение правил эксплуатации;
- Современность заточки;
- Количество распиленного материала;
- Наличие оборудования для заточки;
- Квалификация персонала по заточке
Что касается последних двух факторов, то сервисный центр может гарантировать максимально качественный результат, только если в нем используется профессиональное европейское оборудование с жидкостным (лучше масляным) охлаждением, позволяющее сохранить: необходимое расстояние между зубьями дисковых пил, упругость и твердость сплава, заводской угол заточки, конфигурацию зуба.
Относительно остальных факторов следует сказать, что качество, например, раскраиваемых плит, а также твердого сплава пил зависит от производителей.
Покупая дешевые плитные материалы, клиент заранее обрекает себя на увеличение расходов, связанных с приобретением большого количества режущего инструмента и его частным обслуживанием. Это связано с тем, что в дешевых плитах часто встречаются разнее посторонние абразивные примеси, (например, песок, камни, металл), которые существенно увеличивают износ инструмента.
Для производства качественных твердых сплавов и круглых пил необходимо сложное и дорогостоящее оборудование, что сказывается и на конечной стоимости режущего инструмента. И здесь от покупателя зависит, приобретет он инструмент от ведущих производителей или решит сэкономить на качестве.
Заточка твердосплавных инструментов предъявляет довольно высокие требования как к абразивному инструменту, так и к станку, на котором она выполняется. Сложность заточки таких инструментов заключается в том, что твердый сплав – хрупкий материал. По этой причине станок должен обладать большой жесткостью и высокой точностью. Даже незначительные вибрации станины, алмазного круга или шпиндельного узла приводят к тому, что на твердосплавном лезвии образуются мельчайшие сколы, которые не видны при визуальном осмотре. Увидеть их можно только под микроскопом. Такое лезвие непригодно к работе. При шлифовании твердых сплавов необходимо также помнить о том, что по сравнению с быстрорежущими сталями они характеризуются пониженной теплопроводностью, поэтому требуют более бережного отношения при обработке.
ОСНОВНЫЕ ПРАВИЛА ЗАТОЧКИ РЕЖУЩЕГО ИНСТРУМЕНТА
Для того, чтобы заточить определенный тип режущего инструмента, сохранив его геометрические параметры и обеспечив длительность работы, на предприятии должен быть заточной станок для этого типа инструмента, при заточке надо пользоваться правильно выбранным абразивным кругом и затачивать инструмент, придерживаясь назначенного режима шлифования. Рассмотрим эти аспекты подробнее.
ТИПЫ ЗАТОЧНЫХ СТАНКОВ
Различают универсальные и специальные заточные станки. На универсальных станках можно затачивать почти все дереворежущие инструменты, но это оборудование должно оснащаться специальными приспособлениями или устройствами для установки и закрепления каждого типа инструмента.
Производительность универсальных станков низкая, к тому же они требуют высоквалифицированного обслуживания.
У специальных станков высокая производительность, на на них, как правило, можно затачивать один-два типа инструментов в широком диапазоне геометрических параметров. Наиболее производительные и легко перенастраиваемые – станки с ЧПУ. Для того чтобы изменить геометрические параметры инструмента, оператору достаточно внести изменения в программу ПК, и заточка будет выполняться в другом режиме.
АБРАЗИВНЫЕ (ШЛИФОВАЛЬНЫЕ) КРУГИ
Правильно выбранный шлифовальный круг обеспечивает как высокую производительность заточки, так и высокое качество заточенных поверхностей, то есть высокую точность геометрических параметров и высокую стойкость инструмента. У шлифовальных кругов, используемых при заточке режущего инструмента, есть ряд характеристик, которые необходимо учитывать при выборе кругов. У алмазных кругов это форма и геометрические параметры; расположение абразивного слоя на поверхностях круга; ширина и толщина алмазоносного слоя, марка алмазов (прочность кристаллов); размеры зерен кристаллов; концентрация алмазов в алмазоносном слое; вид связки.
Основные геометрические параметры шлифовального круга: наружный диаметр диска, посадочный диаметр, размер вдоль оси вращения, форма диска, ширина алмазоносного слоя. Абразивный слой, содержащий зерна алмазов, может быть расположен на поверхности диска или на торце. У слоя бывает плоская или криволинейная рабочая поверхность. Плоская рабочая поверхность может быть расположена только перпендикулярно оси вращения. Большинство поверхностей режущих зубьев деревообрабатывающего инструмента затачиваются плоской поверхностью шлифовального круга, то есть у такого шлифовального инструмента абразивный слой определенной ширины и толщины расположен на периферии металлического корпуса круга.
В других случаях может использоваться шлифовальный инструмент в Фоме цилиндра или конуса (например, для заточки пил с дупловидной формой зубьев). У некоторых типов кругов две рабочие поверхности: на торце и на периферии диска; круги также могут быть двухслойными – для чистовой и черновой заточки.
Для изготовления алмазных кругов используются зерна алмазов разной прочности: AC 4, AC 6, AC 15, AC 20, AC 32 (в порядке возрастания прочности). Наибольшее применение при изготовлении шлифовальных кругов находят алмазы AC 4, AC 6.
Производят алмазные круги восьми диапазонов зернистости. У самых крупных диапазон зерен 250 / 200 мкм, у самых мелких – 50 / 40 мкм. От размера зерен зависят: шероховатость обработанной поверхности, в некоторой степени производительность шлифования и даже температура в зоне резания. Чем мельче зерна, тем меньше шероховатость обработанной поверхности, но и меньше глубина шлифования при одном проходе, то есть ниже производительность. Глубина шлифования за один проход не должна превышать 1 / 3 размера алмазного зерна. Иногда имеет смысл разделить процесс заточки на новую и чистовую обработку, например, если накапливается много сильно изношенного инструмента.
Черновое шлифование выполняется кругом с высокой зернистостью алмазов, например 160 / 125, и шероховатость заточенных поверхностей может достигать 1,25 мкм. При чистовом шлифовании кругом с зернистостью алмазов 80 / 63 может быть получена шероховатость 0,32 – 0,16 мкм. Как правило, в хороших сервисных центрах заточку зубьев пил выполняют с использованием алмазного инструмента именно с такой зернистостью, что особенно эффективно при обработке большой партии режущего инструмента одного размера.
Заточка твердосплавного режущего инструмента возможна только с помощью шлифовальных кругов, у которых рабочий слой состоит из алмазов определенной прочности и зернистости, а связка – органическая или керамическая. При увеличении зернистости увеличивается высота нервностей шлифованной поверхности, то есть возрастают шероховатость и в то же время повышается производительность шлифования. Поэтому необходимо выбирать оптимальную зернистость для каждого случая заточки.
Для заточки круглых пил чаще всего используют круги с зернистостью алмазов 80/63 или 120/100, прочностью, соответствующей AC 4 или AC 6, и с условной концентрацией алмаза 100%. В качестве связки алмазоносного слоя обычно используются органические вещества с наполнителем из карбида бора (типа B 2-01 или B 1-02). Такие связки могут обновлять режущую способность рабочей поверхности шлифкруга при падении режущей способности зерен абразива (алмазных зерен). Круги с алмазным слоем на керамической связке обладают большей жесткостью, но могут быстро засаливаться, и их необходимо чаще зачищать – «шарошить» (то есть удалять налипшую стружку специальной шарошкой).
Необходимую форму и размер шлифовального инструмента, а также расположение алмазоносного слоя выбирают в зависимости от положения поверхностей, которые необходимо шлифовать. Например, при заточке дисковых пил с напайными твердосплавными пластинками по задней грани, легкодоступной для шлифования, можно использовать такие круги, как 12 A 2-45 градусов, 12 A 2-20 градусов, 4 A 2 и даже 11 A 2 с алмазоносным слоем на торце. Заточку по передней грани можно выполнять только кругами формы 12 A -200 и 4 A 2, так как величина шага зубьев и размеры межзубного пространства ограничивают размеры круга вдоль оси его вращения.
Наиболее важными параметрами режима шлифования при заточке твердосплавного режущего инструмента, определяющими как качество обработанной поверхности, так и производительность процесса заточки, являются:
- Скорость резания ( V, м/с), то есть скорость движения круга вдоль затачиваемой поверхности;
- Продольная подача ( S, м/мин);
- Глубина снимаемого слоя за один проход круга вдоль затачиваемой поверхности (глубина шлифования h, мм).
Скорость резания определяется диаметром шлифовального круга и частотой его вращения. При назначении скорости резания следует учесть, что разработчики заточных станков используют рекомендации исследователей процесса шлифования по назначению скорости резания и предусматривают, какие материалы будут обрабатываться на станке и какого диаметра шлифовальные круги могут быть использованы на этом станке. Поэтому в большинстве случаев при эксплуатации заточных станков, выпускаемых разными фирмами, частота вращения круга одна, в лучшем случае две-четыре. Кроме того, выпускаются шлифовальные алмазные круги стандартных диаметров – 125 и 150 мм . Если у заточного станка две частоты вращения круга, то при использовании заточных кругов разного диаметра модно обрабатывать инструмент на четырех – шести значениях постоянной скорости резания, что положительно сказывается на выборе режимов резания.
При заточке режущего инструмента, оснащенного твердосплавными пластинами, рекомендуется выполнять шлифование со скоростью резания 8-20 м/с для кругов на металлической связке, 18-28 м/с – для кругов с органической связкой и 18-20 м/с – для кругов с керамической связкой. Если технологический процесс предусматривает получение малой шероховатости на затачиваемых поверхностях, то есть доводку, то используются шлифовальные круги с зернистостью 50/40 или 63/59, при этом скорость резания может быть 30-40 м/с.
Пилы, заточенные с использованием разных способов доводки режущей кромки и качественным шлифованием передней и задней кромок зуба, весьма стойки в процессе эксплуатации. Это связано, в частности, с тем, что у лезвия зуба минимальный радиус закругления (для твердого сплава он достигает 5 мкм), кроме того, при пилении уменьшается разогрев (от трения стружки по поверхности твердосплавной пластинки и корпуса пилы), что повышает стойкость режущих кромок и увеличивает срок работы инструмента между переточками.
Скорость продольной подачи (надвигания круга на зуб) очень сильно зависит от толщины и объема слоя, снимаемого за один проход, что определяется величиной износа инструмента; скорость может составлять 1-3 мм/с (для заточки по задней грани – 3 мм/с, по передней – 1 мм/с. Минимальный съем твердого сплава по передней грани связан также с тем, что качество (шероховатость) поверхности будет в данном случае выше, и это скажется на уменьшении трения стружки о зуб пилы и снижении разогрева корпуса пилы в процессе пиления. При заточке без доводки глубина снимаемого слоя за один проход может быть 0,08 – 0,3 мм . Меньшие величины соответствуют условиям обработки, когда длина дуги контакта алмазных зерен с затачиваемой поверхностью большая – свыше 10 мм . Например, при заточке зубьев дисковых пил с напайными зубьями, ширина которых не более 4,5 мм , толщина снимаемого слоя может быть доведена до 0,3 мм . Производители пил для форматно-раскроечных станков рекомендуют следующие величины съема при заточке: по передней грани зуба – 0,005 – 0,008 мм , по задней грани зуба – 0,2 – 0,3 мм , в зависимости от износа режущих кромок и при обязательном охлаждении. При таких режимах заточки будет обеспечено оптимальное соотношение ресурса пилы и затрат на ее обслуживание.
При доводке пил толщина снимаемого слоя за один проход – 0,005- 0,01 мм , а скорость продольной подачи – 0,5 – 1,0 мм/с.
Увеличение толщины снимаемого слоя за один проход и увеличение скорости продольной подачи ведет к ужесточению теплового режима шлифования и большим температурным напряжениям в поверхностном слое затачиваемого инструмента, что может вызвать появление трещин и прижогов, снижающих прочность режущего инструмента.
Приведенные выше значения толщины снимаемого слоя и скорости продольной подачи рекомендуются при использовании интенсивной подачи смазочно-охлаждающей жидкости (СОЖ). Если же заточка ведется без СОЖ, необходимо снизить скорость продольной подачи и уменьшить толщину снимаемого слоя за один проход. При этом производительность шлифования снижается в два-три раза.
ОХЛАЖДЕНИЕ ИНСТРУМЕНТА ПРИ ЗАТОЧКЕ
В процессе абразивного шлифования различают мгновенную температуру шлифования и установившуюся, или среднюю, температуру, распространяющуюся на значительный объем затачиваемого инструмента. О последствиях мгновенных тепловых импульсов абразивных зерен подробно можно почитать в специальной литературе.
В отличие от мгновенной, установившаяся температура невысока и не может вызывать фазовых превращений металла. Однако в результате нагрева поверхностных слоев затачиваемого инструмента (что неизбежно происходит при шлифовании) в его теле создается перепад температуры. 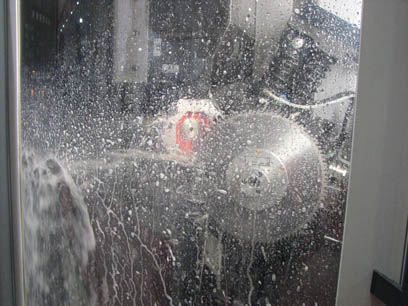
Например, в инструментах с большой длиной лезвия (строгальных и лущильных ножах и .т. п.) перепад температуры по ширине ножа приводит к деформации режущей кромки. В процессе шлифования задней грани в результате нагрева обрабатываемой поверхности на ноже
образуется выпуклость в сторону режущей кромки. Выпуклость при заточке стачивается, и лезвие в этот отрезок времени становится прямолинейным. После заточки, когда нож остывает и температура выравнивается, образуется вогнутость лезвия, величина которой зависит от количества тепла, выделяющегося в процессе шлифования, и интенсивности его отвода из инструмента с помощью СОЖ.
В круглых пилах длина лезвий не очень велика, однако при их заточке без СОЖ могут возникнуть аналогичные проблемы, связанные с изменением структуры как пластинки, слоя припоя, так и корпуса пилы, что может привести к проблемам при ее эксплуатации. Интенсивность отвода тепла зависит от размеров инструмента, зажимных устройств и способа охлаждения.
При помощи охлаждения затачиваемого инструмента жидкостью можно влиять на установившуюся температуру и существенно уменьшать коробление лезвия, снижать риск возникновения шлифовочных трещин и выкрашивания инструментального материала на лезвии.
При заточке твердосплавных пил без охлаждения, на большой скорости подачи и (или) при съеме за один проход большого объема твердого сплава может произойти чрезмерный разогрев твердосплавной пластинки и, как следствие, испарение из нее связки – кобальта, что приведет к полной утере основных свойств твердого сплава – прочности и жесткости. Пилу после такой «заточки» можно выбраковывать.
Подводя итог выше сказанному, подчеркнем еще раз: высокое качество заточки достигается при соблюдении следующих основных требований:
- Правильного выбора характеристик шлифовального круга по зернистости, связке и форме;
- Назначения оптимальных режимов шлифования (скорости резания, скорости продольной подачи, глубины шлифования и применения охлаждения);
- Наличия опытного и подготовленного персонала на заточном участке;
- Использования специальных тяжелых и автоматизированных заточных станков.
|